Fast-track design and build, remodelling and alteration of a 20-year-old, 30,000m² distribution centre in Newbridge into a turnkey, state-of-the-art, beverage concentrate production facility.
Project Overview
The project comprised of the fast-track design and build, remodelling and alterations of a 20-year-old, 30,000m² distribution centre in Newbridge into a turnkey, state-of-the-art, beverage concentrate production facility for an American multi-national client. This included applying for all the Local Authority, utility connections and statutory permissions along with the coordination, construction, commissioning, qualification, and validation activities on site.
The works comprised of:
- Full below-ground process drainage network feeding into a new waste-water treatment plant
- Significant steel frame strengthening works and structural modifications
- New Industrial floors throughout
- Modified façades
- Formation of new Ingredient storage facility and bulk storage tanks
- Construction of new industrial coldrooms and freezer for ingredient storage
- Fully automated beverage processing plant, including batch rooms, blending tanks, fill tanks and packing capability
- Construction of new chilled/freezer/ambient storage areas, batching and product processing rooms, QA/QC rooms, laboratories and associated plant, electrical and other ancillary rooms
- All associated utility systems for the process mechanical works – steam boilers, compressed air, treated water, LPHW systems, HVAC etc.
- All process mechanical and electrical and instrumentation works
- Construction of a new tank farm, tanker unloading area and pipe bridge infrastructure for the unloading and storage of concentrate ingredients
- Construction of a new wastewater treatment facility, a fire-water storage facility and pumping station
We leveraged the latest VDC technology to coordinate and plan complex installations and identify off-site manufacturing opportunities that would de-risk delivery on the ground and optimise productivity. Additionally, with the US based design teams unable to travel to site due to Covid-19 pandemic restrictions, virtual design and tracking tools were widely used to facilitate communication and review of the progress of works, thus maintaining a collaborative and engaged environment between site and design teams. These tools included Openspace 3D tours to track progress, 3D scanning of as-built installations, and detailed modelling of the entire plant.
Key Features
- Turnkey, design and build, and conversion of an existing warehouse, including full mechanical, electrical, instrumentation, process and refrigeration
- Early contractor involvement from project concept stage including responsibility for planning and statutory submissions and permits
- Design, build and commissioning of full utility systems including steam, RO water, HVAC, compressed air, chilled water, LPHW, DCW & DHW, high pressure water, sanitary wash, and detergent systems
- Design assist, installation, verification and commissioning assistance for process mechanical, electrical and instrumentation
- Extensive high purity stainless pipework installation
- Coordination and installation of c. €60m of OFCI equipment including tanks, pumps, homogenisers, CIP centre, powder induction system, and valve matrices
- Coordination and completion of passivation to full process system
- Coordination of energy management system during turnover, start-up and commissioning of process and utility systems
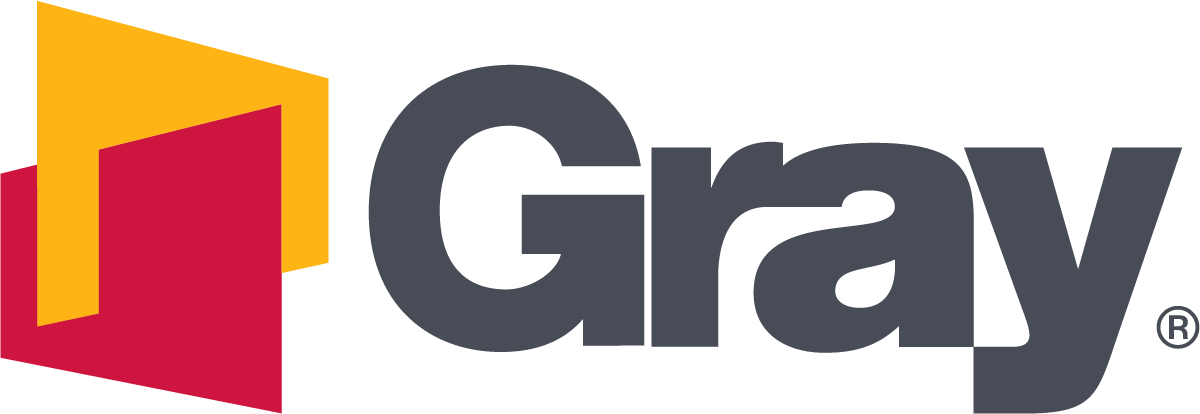
Project Team
Client:Gray Construction working for Keurig Dr. Pepper
Architect:
TOT Architects
Quantity Surveyor:
Gray ISI (USA)
Structural Engineer:
J.B. Barry and Partners
M&E Consultant:
Callaghan Engineering
Project Details
Contract Value:€90 Million
Floor Area:
34,191m²
Duration:
18 months (Multiple phases)